Making Modular in NY: Interview with Eric Bunge
There’s nothing New Yorkers can’t do. Except, perhaps, live in less than 37 square metres. This may be about to change at Carmel Place, an all-modular residential tower completed in 2016 by nArchitects, winners of the adAPT NYC competition launched by then Mayor Michael R. Bloomerg, a pilot programme to develop a new model of housing for downsized households”.
The New-York based office, founded in 1999 by Eric Bunge and Mimi Hoang, has proposed proposed ‘My Micro NY’ (now ‘Carmel Place’), a 9-storey building containing 55 flats ranging from 24 sq.m to 33 sq.m. The architects took a good idea to its logical conclusion: the development is entirely modular.
Carmel Place was one of the projects chosen by Philippe Starck, guest editor of AA new issue, who chose to talk to the editors about modularity and the industrialisation of housing, in aid of quality and housing for all. To complete the article published in this new issue, Eric Bunge agreed to answer our questions.
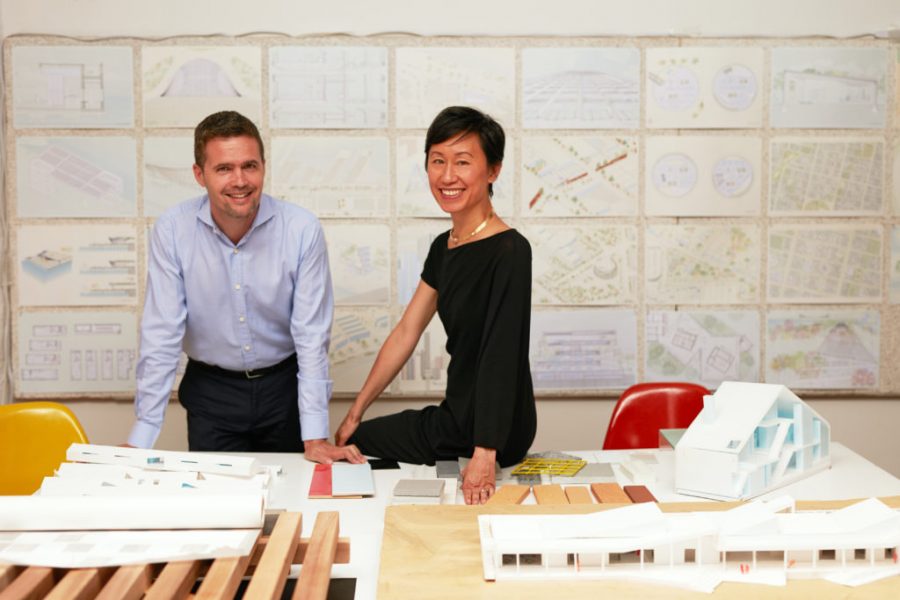
AA: Why did you choose the prefabricated modular for your application to aDAPT NYC? Was it for cost reasons? Was it a request from the city?
Eric Bunge: When we were approached in 2012 by our developer partner Monadnock Development to join their team as the architect, in response to an RFP issued by the city for the city’s first microunit building, the developer asked us if we were up for the challenge to work with their modular company Capsys. We enthusiastically said yes! So we designed the building as a modular building for the competition. While the city didn’t ask for modular construction, it’s very likely that this aspect of our competition entry was one of a few important reasons for our selection.
The developer’s reasons for using modular construction were: proving that a taller building could be built with their system (at the time of completion it was the tallest modular building in Manhattan, though only at 10 stories) ; using a quiet construction system given the dense neighborhood ; quality control in the factory. We were able to build to a 1/8” (3mm) tolerance, which was important since we were very close to the minimum code dimensions for a habitable room – this helped us not lose a vertical line of units. Cost was a factor, but at a relatively small size (55 units; 65 modules), the cost of a modular building is not less than traditional construction in NYC.
AA: Was this use of the modular system a first for you?
EB: That was our first modular project. We built a modular retail village in Boston, and are now building a CLT house. But it’s been difficult finding the right client – most developers assume that modular is inexpensive, which it would be at a larger scale.

AA: What are for you the advantages and disadvantages of prefabrication?
I would say the advantage are the speed of conducting parallel construction sites (the site and the factory), the fast stacking time (the building was stacked in 3.5 weeks) in theory means less noise and great speed. However, as a prototype, with many complicated site conditions and other issues, this particular project was built with a normal construction schedule (despite the fast stacking time). A smaller, skilled labor force is working on a few modules at a time in the factory, rather than a larger force spread out over the entire jobsite. And of course, a potentially very sustainable way to build.
Regarding the disadvantages, construction industry is not yet familiar with modular construction; for instance, the electricians, or painters, don’t always understand that they need to come back to the site once the modules are stacked. Some of the work makes sense on site. You also have to bear in mind that the module size limitation, based on width of truck/route. The distance from factory can offset some of the potentially lower carbon footprint. Limited pool of modular fabricators still makes it challenging.
AA: There was a lot of talk about this project because it lowered the surface standards in housing. Do you know if the City has decided to go further in ordering this type of housing building?
The minimum unit sizes changed in 2016 from 400 sf to 325 sf for senior housing. Carmel Place was part of the conversation, but there were many debates, voices, etc. – the project didn’t lower the area minimums on its own. The city however didn’t change the density factor (typically 680, which is like an average sf area of units in a building), which means that in practice developers can’t build that many smaller units. If they build some smaller units, the other units in the building have to be larger.
The city doesn’t “order” housing in NYC, except as part of the NYCHA housing projects, most of which were built in the 1960s-70s. HPD’s (Housing and Preservation and Development) way of building housing is through financing models, or by disposing of land to developers in return for building affordable housing. They were the lead agency on the city side for Carmel Place, and together with the Mayor’s office, ran the competitive request for proposal.
- Anastasia de Villepin



